Power generation process of the waste-fired power plants
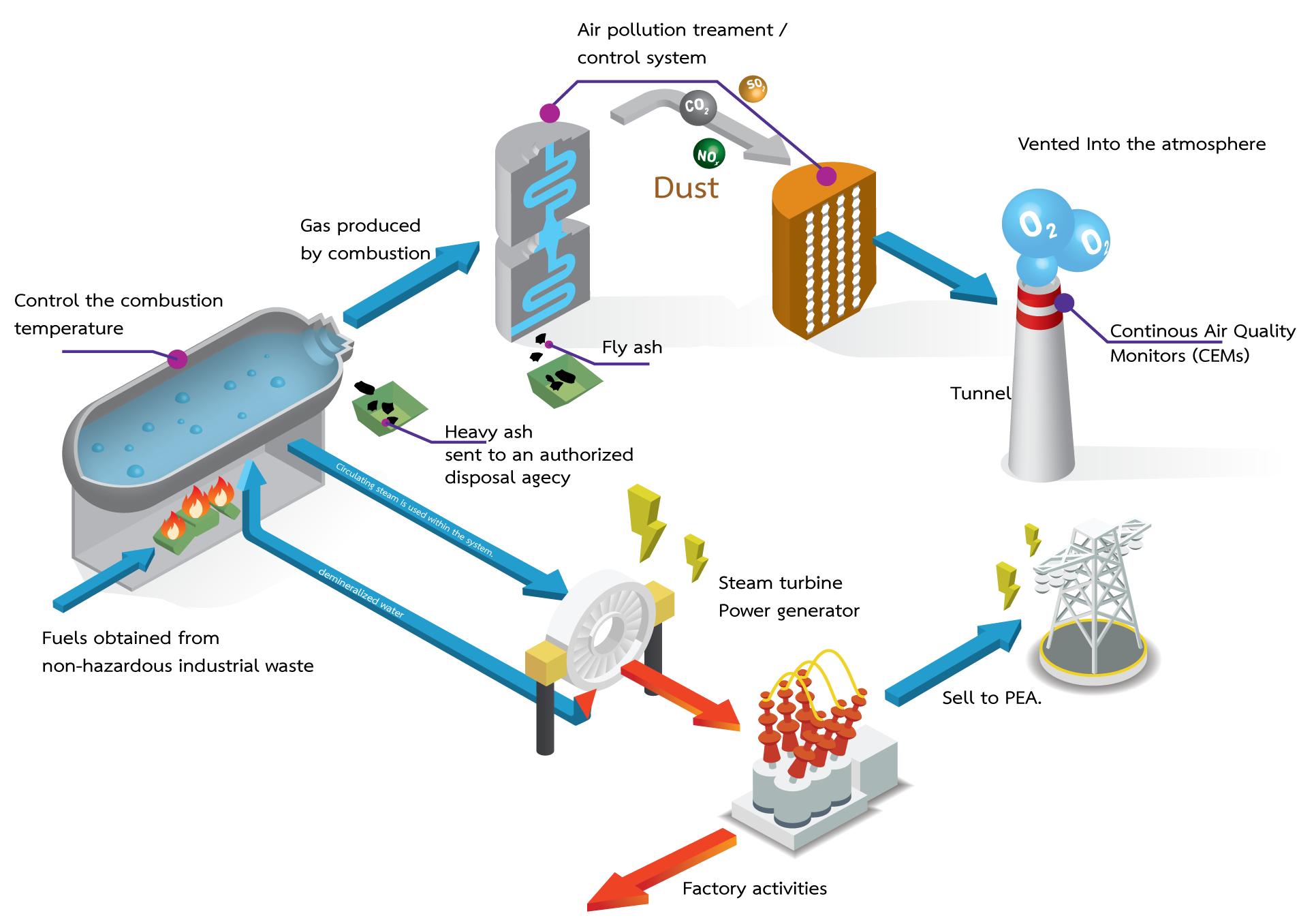
The process of power generation of waste-fired power plants begins with raw water from the water supply system within the industrial estate through the water treatment plant to obtain demineralized water to feed into the steam generator (Boiler). SRF fuel, chopped waste up to 10 cm in size, either in lump or in bulk, as well as in plastic sheets to prevent odors or scattering of waste during transportation to the Company’s power plants. SRF fuel packages are then placed on conveyor belts and the plastic packaging is shredded by machine to distribute the SRF fuel fragments on an inclined belt conveyor before it is fed into the combustion chamber by using step grate system. When the fuel steps are driven into the combustion chamber and the steps are turned over, the bottom of the unburned fuel element on the stepped sludge is turned upward. This causes the fuel parts to ignite and burn completely. In addition, adjusting the speed of the hydraulic stepping unit will help the combustion to be perfectly suitable for each type of fuel, which can be shown in the figure below.
When the SRF fuel is completely burned and turned into ash. The nature of this ash can be divided into two types: heavy ash (bottom ash) and light ash (fly ash), in which heavy ash falls to the bottom of the combustion chamber where it is collected and stored in the ash storage tank before sending further for ash disposal. The remaining ash is burned away in hot air, also known as light ash. It is trapped by an electrostatic precipitator (ESP) and transported to the ash collection chamber before further disposal by the contractor. However, light ash contains no toxic substances and hence can be utilized, for example, landfill disposal with acidic properties to be treated with alkaline ash, etc.
During combustion it generates heat which makes the demineralized water in the boiler to be converted to superheated steam (Super Heater) which steam will rotate the blades of the steam turbine that has the same shaft axis as the generator to generate electricity and the voltage is adjusted by a transformer to the level of 22 kV in order to be able to supply electricity to the power grid under the Power Purchase Agreement with PEA. The superheated steam will then be condensed in the condenser by using cold water from the water storage tank and tower (Cooling Tower) allowing these waters to be sent back into the boiler to continue to produce steam. However, the effluent from the production process does not contain harmful toxins though it will still be treated with only chemicals or coagulants before storing them in the reservoir and forwarding to the evaporation pond to evaporate naturally, or to be reused such as for watering plants, washing the road, etc.
-
Complete fuel combustion system using high heat.
-
There is a modern air treatment and purification system. Both bag filter system and wet scrubber
-
There are continuous chimney air quality monitoring systems (CEMs) and display 24 hours a day. The ash produced by combustion has been properly disposed of. by factory license number 101 only
-
Use water from the water supply system of Kaeng Khoi Industrial Estate.
-
Wastewater from office buildings will be collected into prefabricated septic tanks for treatment to meet the specified standards.
-
Wastewater from cooling systems, boilers and RO systems will be entered into the sewerage pond for quality inspection
-
Wastewater in the sewerage pond will be reused. in watering green areas within the project area
-
Stable energy to support tourism and occupation in the area
-
Community Development and Education Fund
-
Local development tax from building a power plant
-
Stimulate the economy by building factories